Author: Nguyen Vo -
For my placement year, I’m lucky to be working with National Oilwell Varco (NOV). The name may not ring a bell to you, but it is one of the largest oil and gas supplying companies in the world. NOV provides equipment ranging from pumps and motors to downhole equipment such as drill strings, stabilizers and blow-out preventers. The facility in Stonehouse, Gloucestershire - where I’m based - is specialised in designing and manufacturing drill bits.
The drill bit design cycle
As a Product Line Engineer (PLE), I’m exposed to a wide range of work. My main role is to design and improve the performance of drill bits, as well as make changes to drill bits to meet a customer’s specifications. When I am tasked with a project, it is my job to manage it through all of the stage gates. At the start of every project a kick off meeting is held, where I discuss with sales colleagues the project requirements and all the parameters needed for analyses. After this, computer-aided design (CAD), finite element analysis (FEA) and computational fluid dynamics (CFD) work are carried out to ensure all criteria are met. Within the design phase, I often have to communicate with other departments for several reasons including to ensure my drill bit is manufacturable and all the materials have been ordered so it can be completed on time.
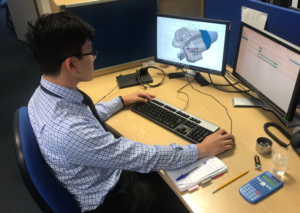
After the design and manufacturing process is done, I inspect my drill bit and sign its final approval. Sometimes, I also get to see my bit run downhole in the field and get feedback from the customers. This all can happen as quick as within two months! As busy as it may seem it’s rewarding when receiving positive feedback and I aspire to break a drilling record!
Some projects require designers to look at dull bits (a term meaning a bit that has been used), evaluate which modes of vibrations have caused failure before making changes to bit to better its performance. Being exposed to the whole design lifecycle from concept to manufactured to performance results is an experience you don’t receive on many placements; none of my friends are getting this experience.
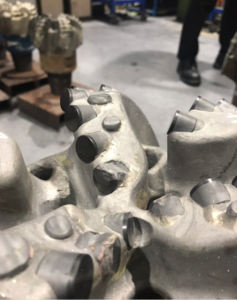
Besides my main roles of designing and inspecting drill bits, I am currently helping improve the CFD templates as we upgrade our systems. This is done by performing multiple CFD analyses and investigating if the results match with what I expect the fluid flow to be. I’m also involved with an innovative project in which I have to provide a downhole data recorder pocket for testing purposes.
Why do I enjoy working for NOV?
First of all, the work is challenging, and it varies day by day. It keeps me busy, which is a big plus. As no two wells are drilled the same way, one day I work on a conventional drill bit, the next day I’ve got a project on a core bit, which is a completely different type of drill bit that requires a different design technique. The minute after, I’m on the phone with someone over in the US giving them software feedback; there are also a lot of occasions I have to go to the shop floor to inspect bits and mould pots. I have learned a lot and gained new skills since August when I first came, not only have I improved design skills but also how to better interpret graphs and finite element results.
NOV has a nice working environment. Everybody, not only my department colleagues but also mechanics on the shop floor, are very approachable and would patiently explain to me concepts I struggle to understand and provide me with all the help I need. The company also has a great social side with football games held every week which bond everyone together. Within the PLE department, I along with three others (who are all graduates from Bath) occasionally watch the local football team Forest Green Rovers.
Fact: engineers in the oil and gas sector are the highest paid in the UK in 2018. Not only has NOV got a competitive salary in the industry (relative to placement salaries at Shell, Schlumberger and Total offered in 2018) but its benefit schemes such as free gym, health package and free vaccinations are all rewarding.
Oil wells are all around the world and so are NOV’s clients; from the Middle East (Oman, Saudi Arabia, UAE, Egypt) to Europe (Norway, Romania, Poland), and even to the Far East such as Thailand, Singapore and Vietnam, there are many chances for you to see the world (and to present your design concept to your clients), which is one of the reasons I want to work for the oil and gas industry.
How to secure a placement role
I’m ending this blog by giving you my top tips I learned throughout second year (the hard way) to get employers to choose you:
- Research about the company. I often get asked in my interviews: ‘What do you know about us?’, so have a flick through companies’ websites and be prepared to surprise them with what you know.
- Smile! Sure interviews are nerve-wracking, but a bit of smiling doesn’t kill you. In fact, smiling makes you more comfortable and employers will see you as a relaxed and friendly person, who probably will work well under pressure.
- Make sure you know your strengths and weaknesses and be able to evaluate, realise there’s room for improvement and show you’re working on it. Employers almost certainly will be impressed.
- Employers usually round up the interview with ‘Do you have any questions?’. In my humble opinion, this is your chance to shine and stand out from other candidates. Don’t just ask ordinary questions, challenge them back with tough questions. Throw them with questions that will make them scratch their heads.
And finally, best of luck securing yourself a good placement!
Respond